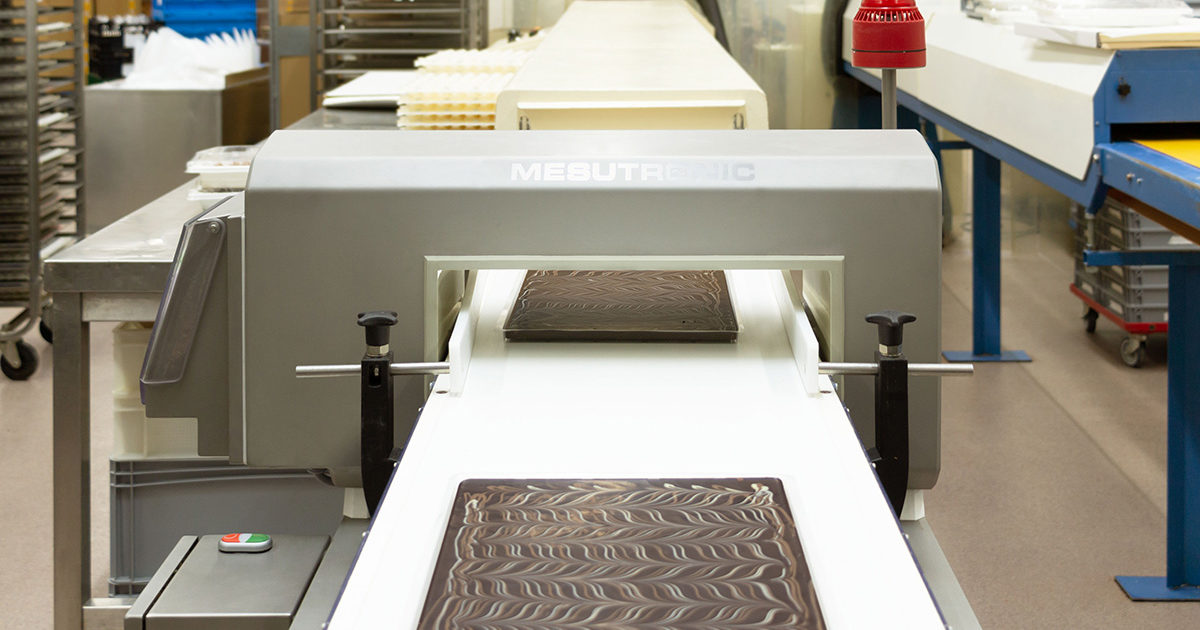
Metal detection – perfectly integrated into the production line
Quality assurance between artisanal and industrial production
For companies with a small-scale manufacturing background, such as Seidl Confiserie GmbH, foreign body management programs must be tailored to the individual production processes. Flexibility, innovation and usability are particularly important here.
From Kenya to the Upper Palatinate
In general, the quality of the food served near motorways leaves a lot to be desired. But not on the A3 motorway between Regensburg and Nuremberg. Right next to the junction for the town of Laaber, you can find delicacies from Africa and all over the world, refined by Seidl Confiserie GmbH. Their story began in the late 80s with Managing Director Johann Seidl’s passion for travel and chocolate.
The first product, an edible milk jug in a delicate light brown, is still an integral part of the product portfolio today. The macadamia nut, whose triumphant progress across Europe’s confectionery shelves began here, is also still one of the cornerstones of the company. In contrast to the modest early days, over 85 employees now process more than 250 tons of raw materials annually, manufacturing a wide variety of products such as pralines, spreads, snacks, chocolates and baked goods.
In addition to ever-growing online sales in Germany, Japan is the next company target. “Unique products of the highest quality, such as our new praline cake, are the key to this. They will help us to gain a foothold in this demanding market,” comments Johann Seidl.
Naturally, continuous growth means upgrading production to industrial standards. Nevertheless, at Confiserie Seidl, the core values of an artisanal manufacturer are still evident. These are crafting skills, an eye for detail, the drive for innovation and, above all, love for the product.
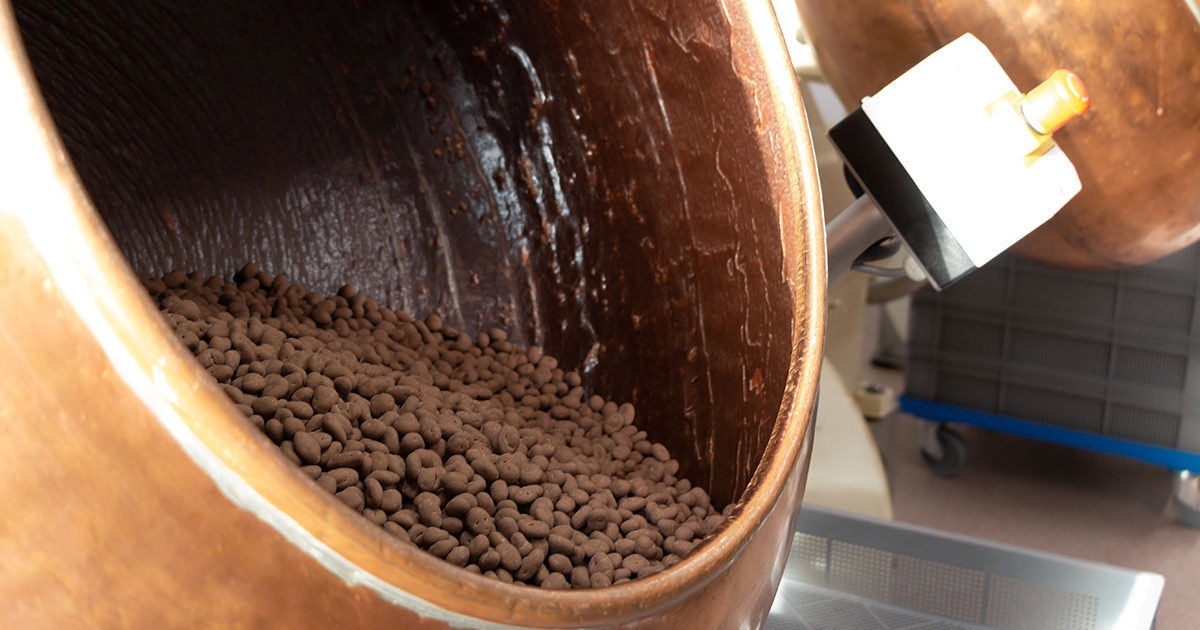
Making good things even better, coating almonds
Small batches result in complex tasks
Expanding the idea of a small-scale manufacturer to over 1,000 individual products in different pack sizes brings unique challenges. Particularly when large quantities of the most popular products have to be produced or large orders fulfilled. Up to 12 different products are run on one line per production shift. Delays in setting-up therefore have a massive impact on daily production. Short and efficient cleaning routines are equally important. Individual customer requests or new types of products have to go into serial production quickly in order to meet delivery times or to satisfy the latest consumer trends.
“Our business is demanding, but it’s never boring,” says Jakob Hilber with a grin. As Marketing Manager, in collaboration with Mr Seidl, he is the person who repeatedly confronts the production department with new creative challenges.
Profitable through tradition and innovation
Various factors are decisive in being able to solve such complex tasks profitably. First of all, your own employees must be flexible and excellently trained. For the majority of products, one or more steps are carried out by hand. This includes filling the cream-cocoa-almonds in the coating drum to delicately writing an individual chocolate telegram.
Just as important is a machine program that is perfectly tailored to our application. At Seidl Confiserie GmbH, lovingly restored older systems are used for special jobs, such as an old fine grinding mill. It is used for the sugar layer of the red-coated peanuts everyone remembers from childhood. By contrast, modern vertical form fill seal machines or pouring stations are also in use. When it comes to quality assurance in particular, the company does not just rely on every employee’s trained eye.
“The high number of manual production stages helps us avoid many quality defects before they occur”, says Johann Seidl, “but there are also problems that cannot be identified by touch or sight.” In a company that processes such a large number of natural products, the presence of foreign bodies is always a relevant subject for risk assessment. For detecting metal, Mesutronic GmbH from Kirchberg im Wald is the partner of choice.
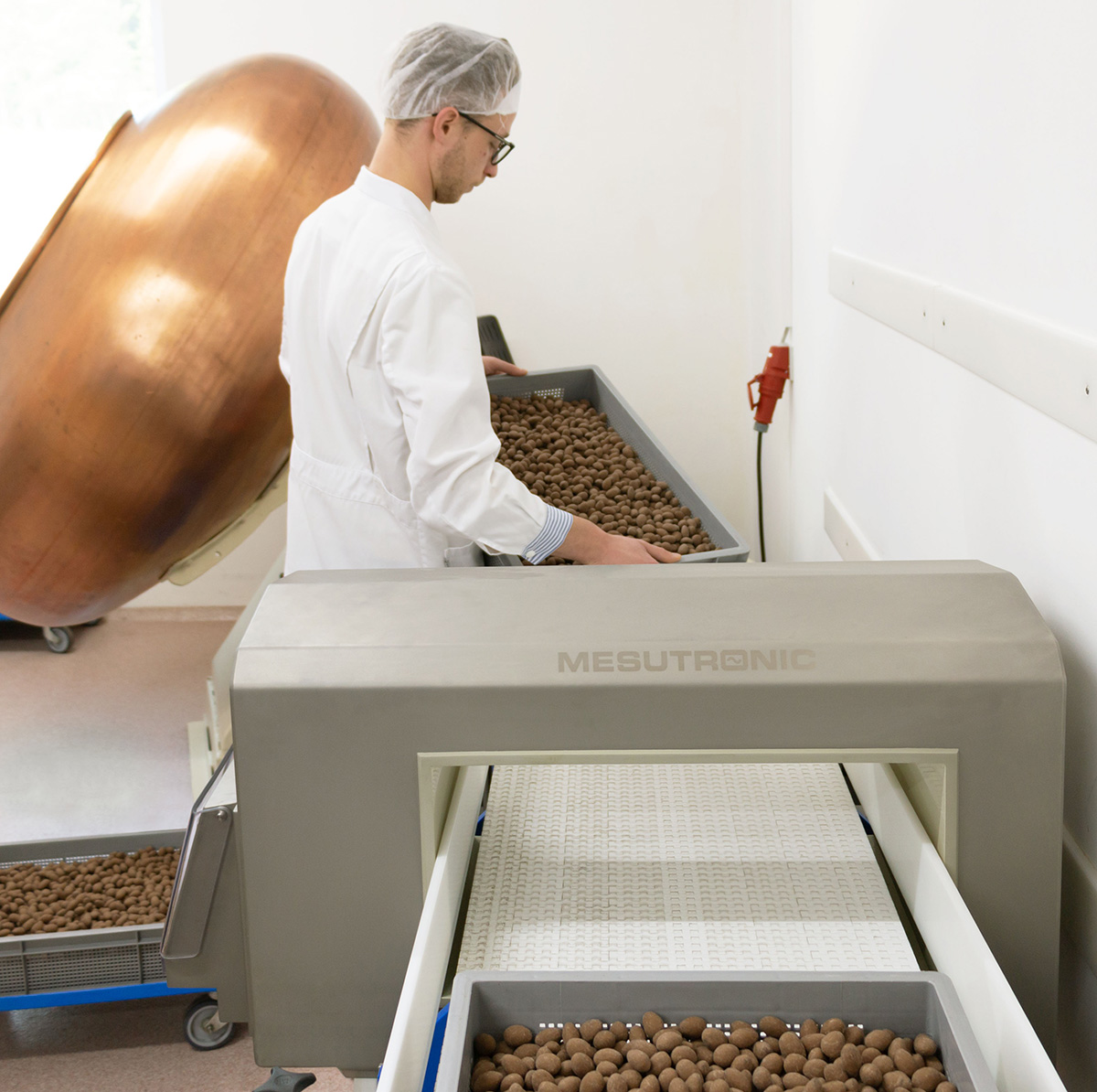
Uncompromising safety for all pack sizes
From specialists for specialists
The METRON 07 CI tunnel metal detectors used on TRANSTRON conveyor belts perfectly meet the requirements of flexibility, ease of cleaning and high performance. Setting up new products is intuitive and quick for every operator. Large, smooth running rollers, guided cable guiding and a design with as few protruding parts as possible enable simple changes of location from line to line while minimizing the risk of damage.
AMD07 electronic series devices boast exceptional performance in detection. In this way, a generous opening size can be chosen in the layout phase without breaking good manufacturing practices. During operation, this allows a broad product portfolio to be examined across minimal different system sizes. Traceable and seamless reporting can be done directly on the machine itself without necessarily having to establish a connection to the company network.
“The requirements of manufacturing companies with an artisanal background are well known to us,” explains Christian Boxleitner, Director of Sales at Mesutronic . “When it comes to machine engineering, we also lean in an artisanal direction. Most of our systems are specially modified for each customer and thereby perfectly tailored to their needs.”
It is precisely this focus on satisfying customer needs to the highest level that unites Seidl Confiserie GmbH and Mesutronic GmbH. This results in a solid partnership, complementing each other like nuts and chocolate.