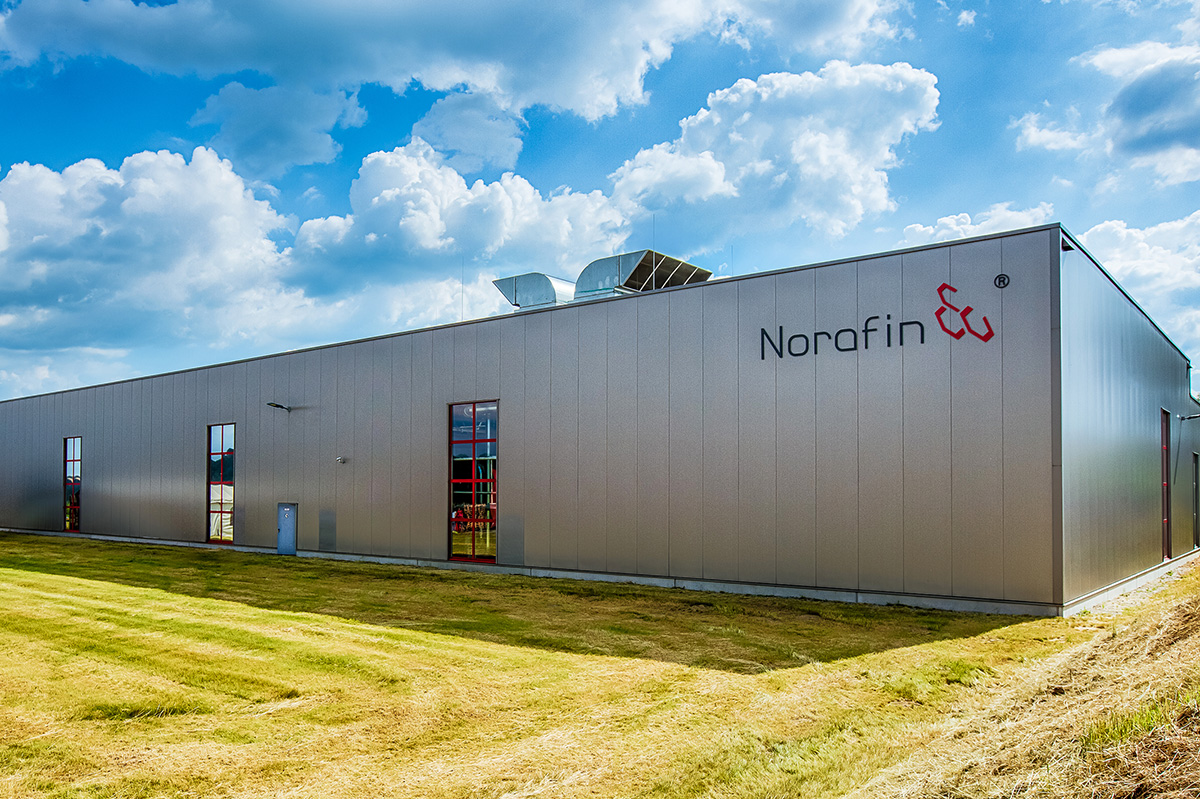
A visit to Norafin Industries (Germany) GmbH, one of the world’s leading manufacturers of special nonwoven fabrics. The company produces innovative, hydroentangled and needle-punched nonwoven fabrics for numerous applications that surround us in many areas of our life as high-tech components. They protect, filter, clean, air-condition and create comfort and safety. Companies such as Norafin therefore make an important contribution to an environment worth living in. To guarantee this high quality, metal detectors are an indispensable aid for plant protection and quality assurance.
The company was founded in 1985 and its headquarters have been in Mildenau in the Erzgebirge (Ore Mountains) since 1997, where it employs 193 people and had a turnover of 36 million Euros last year. In 2018 the company completed the construction of its production facility in Mills River, North Carolina, USA. 36 employees found a new workplace on a floor area of 7,000 m². And not only that: with the construction of a production facility in North America, the company can offer an even better service to its customers, which include a company that makes protective clothing, and further expand and strengthen its position in the market. For instance, almost every protective jacket used today by the fire department in the USA already contains a heat and fire-resistant protective barrier made of nonwoven fabric from Norafin. “When the fire department’s operatives go out to fight fire, their protective suits often contain 2 to 3 layers of the Norafin product”, explains Norafin’s CEO André Lang. Other, but no less demanding quality criteria apply to other applications in the fields of industry, medicine, composites and filtration. “Whatever our customers demand from us, that is also precisely what we expect from our partners. That’s why we only cooperate with the best”, says André Lang.
When it comes to metal detection, the company relies on Mesutronic GmbH from Kirchberg in Wald, Lower Bavaria, Germany, which leads in the textile industry with its metal detectors. To achieve optimum process and quality assurance, beam and flying conveyor detectors are used in the different process stages of the nonwoven fabric production. Primary, artificial and natural fibres are used, which are manufactured according to a proprietary recipe – free from metallic contaminants.
However, fibre openers and carding machines with metallic tools are used in the further processing, e.g. for cutting open bales and manufacturing the nonwoven fabrics. If these tools break, they can not only negatively affect the properties of the product, but also endanger the entire production. For that reason Norafin uses the Metron 05 Powerline metal detector in the fibre transport. This detector can be inserted directly into the pipeline. Metals can also generate sparks in these areas and thus start a fire. Metal detectors and spark detectors are therefore often integrated together in pipelines. Through their use at the start of production, the ingress and distribution of metal contaminants in the further process can be minimised without the risk of having to scrap finished nonwoven fabric.
In the subsequent manufacturing process, needle punching and extremely variable hydroentanglement take place for the specialisation of the nonwoven fabric. With mechanical needle-punching, the downstream production plants are normally protected by beam-shaped metal detectors. Damage to the plants caused by needle breakage are usually very expensive and the loss of production in the case of a high production density can barely be compensated.
In accordance with Norafin’s strict quality assurance concept, the nonwoven fabrics are guided over a segmented detector at the end of the manufacturing process before being made up. Very fine metal parts such as a broken fragment of the tip of a needle are reliable detected with this system of the type Metron 04 Profiline. Depending on the version, the position of the foreign body can be located with an accuracy of 300 or 150 mm. The detection system can operate without any problem under the varying process conditions with production speeds of up to 2 m/s and product temperatures of up to 120 °C.
Those who manufacture components for protective equipment, sterile covers for operating theatres in hospitals, room air filters and even flax wallpapers for improving the room climate are working at the high end of nonwoven fabric development. The high expenditure and extraordinary quality standards that are characteristic of the production at Norafin resulted in 2017 in the company winning the award for the best product in the category “Industrial Textiles” at the Future Textiles Awards, which are presented by the World Textile Information Network (WTiN). A key factor in the attainment of such high quality goals is the selection of suppliers that share these goals. Mesutronic is Norafin’s partner when it comes to metal detection.